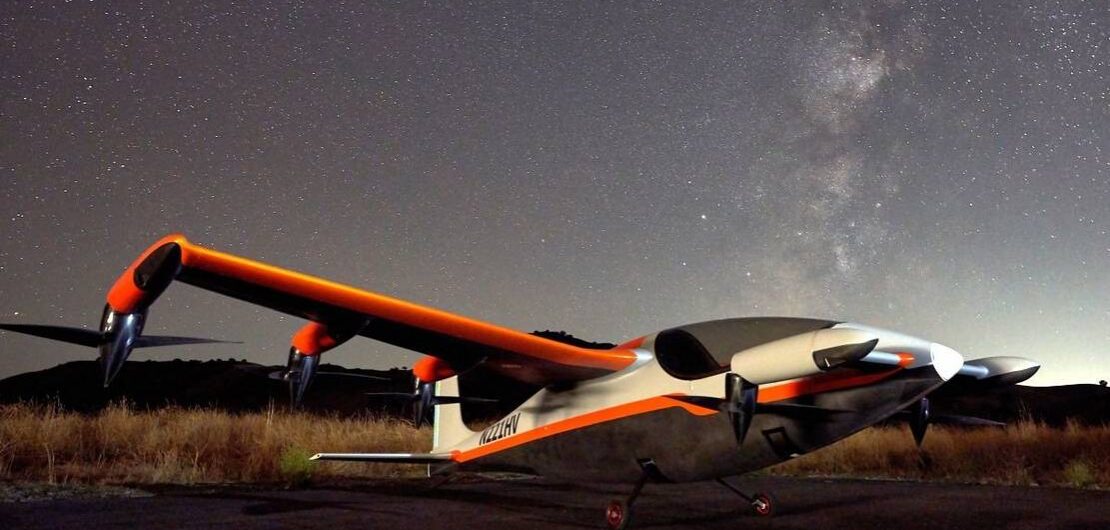
Heavyside
Our client requested SDC to design and build carbon fiber structural panels which would incorporate custom components (provided by the client) as part of a next generation defense weapon.
Phase 1
I was given the task of managing the proof of concept project for 3 different configurations of composite panels with embedded elements. If successful, the project would transition to a production development phase, so schedule and customer satisfaction were key requirements for the project.
My tasks consisted of running weekly status meetings with the customer, creating and maintaining a detailed schedule and budget, purchasing all material and tooling, writing a
San Diego Composite
San Diego Composites is small manufacturing facility which creates specialized metal and composites aerospace parts in San Diego, CA. I started as an intern while completing my Structural Engineering degree at UC San Diego and joined San Diego Composites upon graduating. I worked on and led several projects for the research and production services of the company.
Composite Panels with Embedded Elements for Leading Defense Contractor
Our client requested SDC to design and build carbon fiber structural panels which would incorporate custom components (provided by the client) as part of a next generation defense weapon.
Phase 1
I was given the task of managing the proof of concept project for 3 different configurations of composite panels with embedded elements. If successful, the project would transition to a production development phase, so schedule and customer satisfaction were key requirements for the project.
My tasks consisted of running weekly status meetings with the customer, creating and maintaining a detailed schedule and budget, purchasing all material and tooling, writing all manufacturing instructions, manufacturing the part with assistance from staff technicians, managing material property testing and inspection, presenting and reviewing the concepts with the client, and finally working with upper management on the Phase 2 proposal to leverage this work into a larger contract.
Phase 2
The second phase of the project was significantly larger in scope with a much larger team and I was assigned to lead the technical development part of the project. The panels changed in complexity by incorporating multiple parts bonded together, co-cured honeycomb and an increase in the number of embedded inserts, consequently, the number of configurations doubled to 6.
The team was tasked to optimize the parts for weight and manufacturability, while staying within the technical requirements for volume envelope, in plane loads and vibrational frequency limitations.
For these new panels, I designed tooling, managed the analysis engineers assigned to the project, performed producibility reviews with the manufacturing team, communicated analysis and producibility findings to the customer, modified designs accordingly, oversaw analysis team’s re-analysis of the new designs, ordered material, wrote manufacturing documentation and led the manufacturing process on the shop floor.
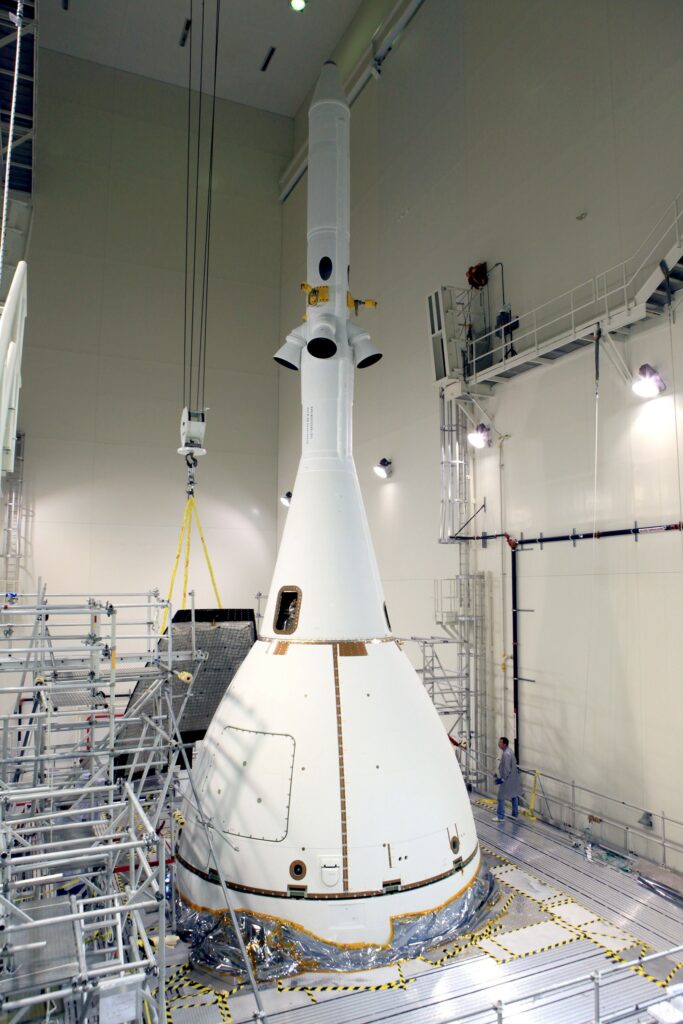
Thermo-protective system and Seals for the Orion SpaceCraft for Lockheed Martin
Lockheed contracted SDC to manufacture parts for the Orion MPCV according to customer furnished drawings and specs. First Round: Thermo-protective Panels I had the opportunity to manage my first end-to-end project. The end goal of the project was to manufacture thermal protective (high temperature insulation) for the Orion MPCV. I purchased the material, wrote the manufacturing instructions, oversaw machining, inspection, and packaging while ensuring the end product met all of the specifications. Recurring work After a successful first contract, I assumed responsibility for writing proposals for the ongoing work and managing each project task after SDC was awarded the work. I continued to do the same work with the addition of writing proposals, interfacing with the customer, and creating schedules and budgets. I branched out from just thermal protective panels to seals and other similar parts for the same customer. Some of these parts were made from very hard to procure materials, so for those, the best solution was for SDC manufacture them and I oversaw the manufacturing, and in some cases built the parts, to ensure quality and schedule were met. I successfully delivered on 14 different contracts for 100’s of parts that will be flown over the next decadeThe Orion Multi-Purpose Crew Vehicle(MPCV) is a US-European spacecraft intended to carry a crew of four astronauts to destinations at or beyond low Earth orbit. The parts I made are expected to launch in 2022.
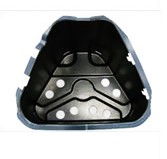
Parachute Buckets for the New Shepard for Blue Origin
Blue Origin contracted SDC to produce additional shipsets of parachute buckets for its New Shepard vehicle My task was to update the tooling to reflect the new designs I redesigned the manufacturing tool so that it could be machined from the old tool to save cost for the customer. I also created a machining fixture for all the finishing work to ensure that the parts remained within the final tolerances while also documenting final matching processes using handwork instead of automated CNC to reduced time and cost. Parts made from the tool I designed are currently being used for testing